Legal requirements for industrial dustfilters in bakeries
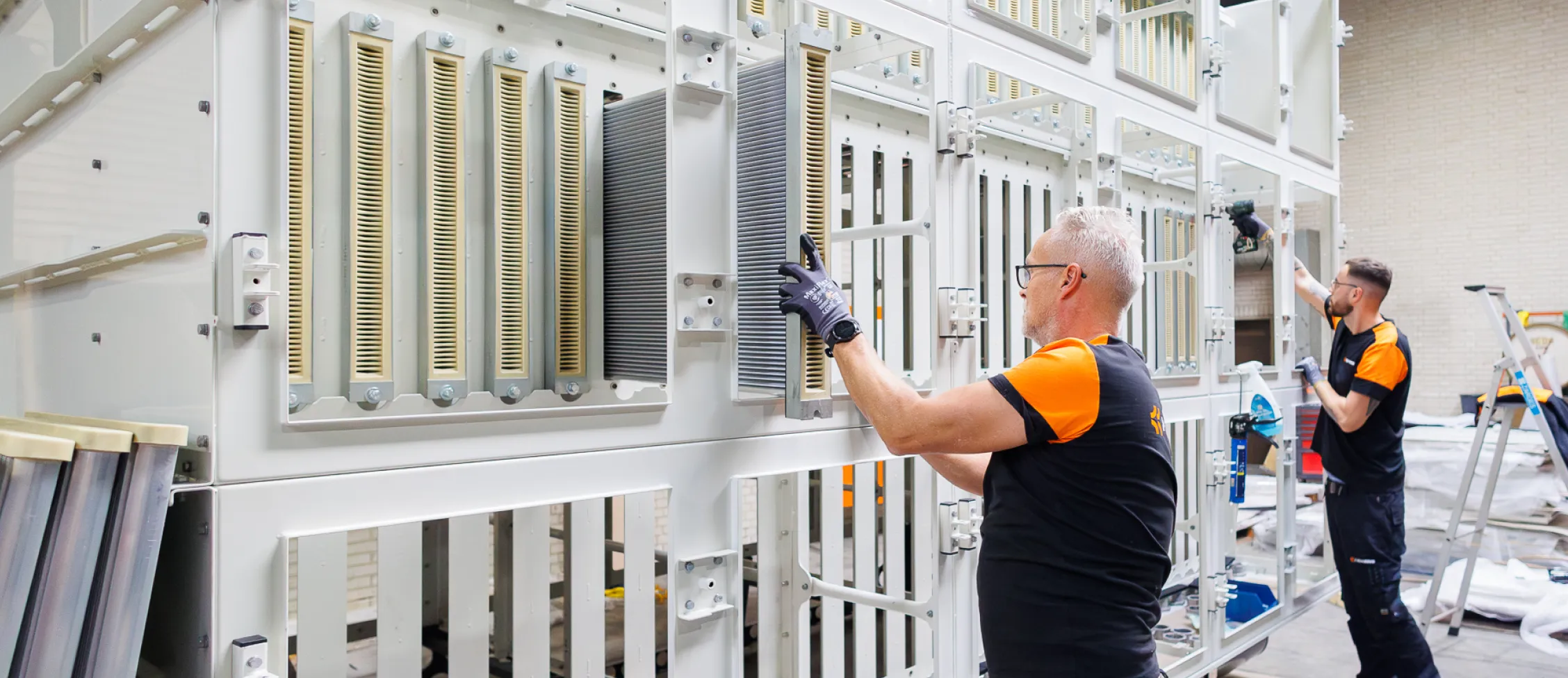
What are industrial dustfilters?
Industrial dustfilters remove harmful substances such as dust, oil mist, vapors, aerosols, and gases from the air, significantly improving air quality. They are essential in industrial and commercial settings to protect workers from health risks. Depending on specific requirements, these systems can be designed for substances like emulsions or biological agents. Extraction solutions come in various sizes and configurations, including both mobile and stationary units.
Extraction technology: obligations and requirements for companies
Companies that use industrial dustfilters are responsible for adhering to strict legal guidelines. This is essential for ensuring employee safety and protecting the environment. Under the Occupational Safety Act, employers must actively promote workplace health and safety—such as by conducting risk assessments and implementing suitable extraction systems. The Dangerous Substances Act reinforces these obligations by outlining safe handling practices for hazardous materials and enforcing workplace exposure limits, further specified by the Technical Guidelines for Hazardous Substances (TRGS). Additionally, the Occupational Safety Ordinance mandates regular inspections and maintenance of extraction systems.
For explosive environments, strict explosion safety regulations apply. Companies must prepare an explosion protection document and use ATEX-compliant systems to mitigate risks. Sustainability is also a key factor—the Federal Environmental Protection Act regulates emissions generated by extraction systems.
For businesses, this means regularly maintaining and inspecting their systems, documenting all safety measures, training employees, and ensuring compliance with exposure limits. With our expertise in extraction technology, you can stay fully compliant with all legal requirements.
Key requirements for industrial dustfilters
The safe operation of dust extraction systems is essential for occupational safety and compliance with the appropriate regulations and standards. In the Netherlands, various laws and guidelines apply. The Occupational Health and Safety Act (Arbowet) requires employers to ensure the health and safety of their employees. The Arbobesluit, specifically Chapter 4 on hazardous substances, provides additional rules for handling substances in the workplace.
Furthermore, dust extraction systems must comply with the Machinery Directive (2006/42/EC) and the Low Voltage Directive (2014/35/EU) for electrical safety. The EMC Directive ensures that your equipment does not cause electromagnetic interference. If you work in explosive environments, you must follow the ATEX directives (ATEX 114 and 153) and prepare an explosion safety document.
Additionally, the PGS guidelines apply depending on the type of dust and activity, and NEN standards such as NEN-EN 689 for exposure assessment are important. Finally, the SER list includes the limit values for hazardous substances that must be met to protect the health of your employees.
The most important guidelines for industrial dustfilters at a glance:
- Machinery Directive (2006/42/EC)
- Low Voltage Directive (2014/35/EU)
- ATEX Directive (ATEX 114 and ATEX 153)
- Occupational Health and Safety Act (Arbowet) and Arbobesluit (Dutch legislation)
- NEN standards (e.g., NEN-EN 689 for exposure assessment)
CE Conformity and Legal Requirements in Europe
Manufacturers of industrial dust filters must issue a declaration of conformity confirming that their equipment complies with European standards. The CE marking indicates that the equipment is suitable for use across Europe and meets all relevant directives, such as the Machinery Directive (2006/42/EC) and other applicable standards like the Low Voltage Directive and EMC Directive. In explosive environments, ATEX-compliant dust extraction systems are legally required and must meet specific fire and explosion protection requirements under ATEX 114 and ATEX 153.
Planning and installation
From the design phase, it is crucial to ensure that the dust extraction systems are suited to the specific operational conditions. This involves analyzing the hazardous substances to be captured, calculating the required airflow volumes, and integrating safety mechanisms such as explosion protection. The design and installation should be carried out by qualified personnel.
Operation, control and maintenance
During operational use, it is essential to conduct regular maintenance and inspections to ensure the functionality and safety of the dust extraction system. For example, filter elements should be periodically checked for wear, and accumulations in pipes and collection containers should be regularly removed. Testing and maintaining control and safety systems is also vital.
Documentation and training
All maintenance and inspection activities must be thoroughly documented, not only as proof for regulators but also to continuously optimize the systems. In addition, it is important to regularly train employees on the proper use and maintenance of dust extraction systems, so they are aware of how the systems work and the importance of maintaining them.
Employee protection
The primary goal of these guidelines is the protection of employees' health. Effective extraction of hazardous substances, such as dust, fumes, or gases, improves air quality in the workplace and reduces the risk of occupational diseases and accidents. Regular maintenance and inspection of the extraction systems are crucial to ensure they continue to operate effectively.
CE compliance and legal requirements in Europe
Manufacturers of extraction systems must provide a declaration of conformity, confirming that the installation meets European standards. The CE mark on a system indicates that it complies with all applicable regulations, such as the Machinery Directive, and can be used throughout Europe. Important: In explosive environments, ATEX-compliant extraction systems are legally required. These systems must adhere to strict fire and explosion protection regulations.
Legal management of welding fumes
During welding, harmful particles are released, known as welding fumes. When certain limits are exceeded, inhalation of these fumes can lead to long-term health issues, such as asthma or lung diseases. In the Netherlands, hazardous substance legislation requires the use of point-of-source extraction systems for effectively capturing welding fumes. General air extraction systems do not meet the legal requirements for welding fume extraction. These point-of-source systems are mandatory for removing harmful substances directly at the source and minimizing exposure to employees.
Compliance with dust extraction regulations with Kiekens
Kiekens has been a leading supplier of modern dust extraction solutions for industrial applications for decades. Whether it's dust, oil mist, or welding emissions – our systems always meet the latest legal requirements and ensure maximum efficiency and safety in any working environment. With our experience, high-quality technology, and customized solutions, we help you not only comply fully with applicable laws and regulations but also protect the health of your employees in a sustainable way.
Contact us to discover how we can make your dust extraction technology future-proof!