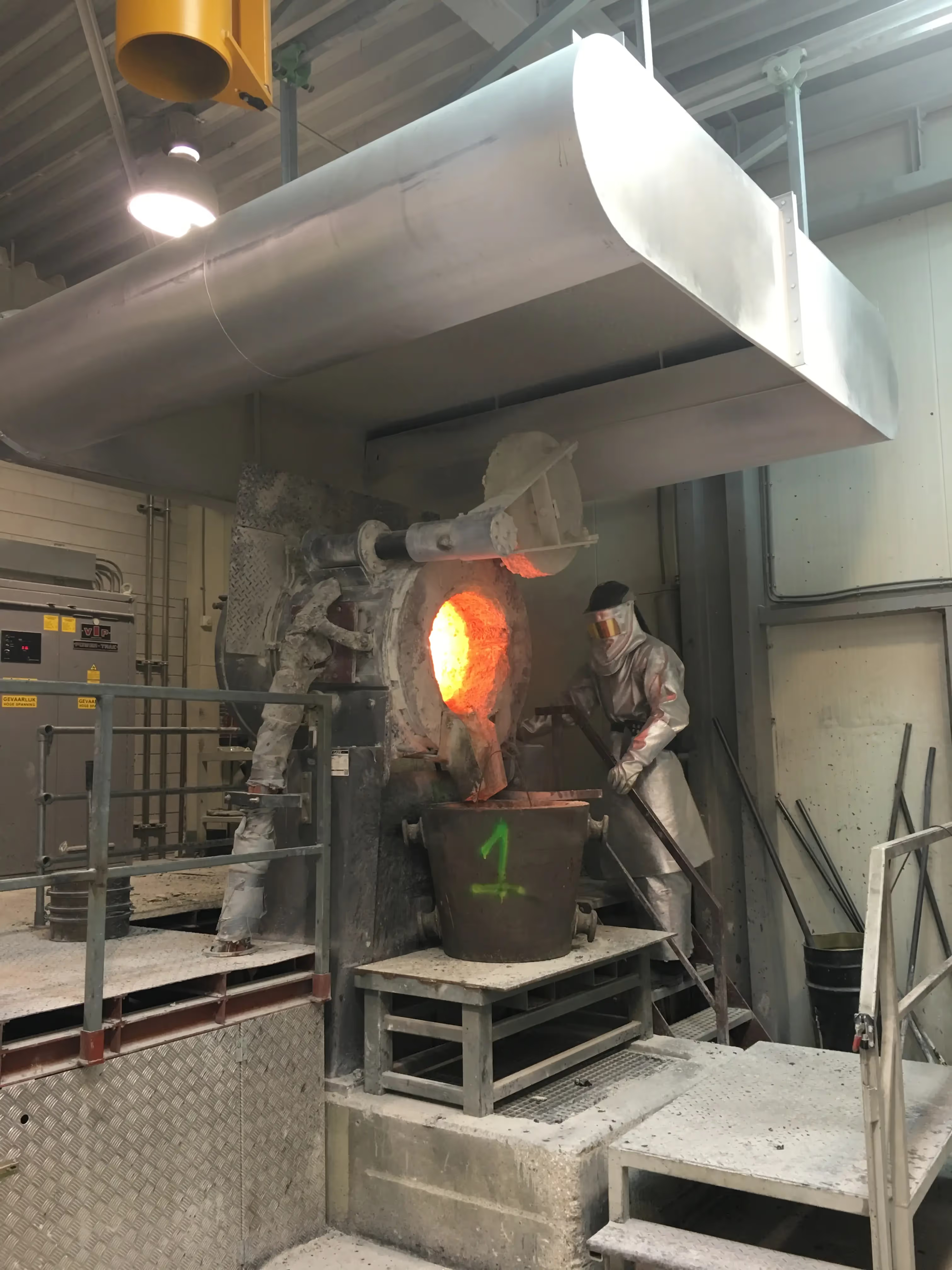
Blue Phoenix: on a sustainable mission in a clean (work)environment
Blue Phoenix practices a sustainable line of business. Through a sophisticated process, this English-Dutch venture resurrects valuable raw materials from raw ash. It starts with processing bottom ashes from various incineration plants. The concentrates that are obtained contain materials such as copper and aluminum. Blue Phoenix then supplies the extracted and cleaned minerals and base metals to copper, gold, and aluminum processors in the Netherlands and abroad. In the midst of this process, Kiekens' Dustmasters play an important role.
Clean workplace, clean environment
Bob Leeftink, General Manager of Metal Production and Sales at Blue Phoenix, explains:
"When metals are melted, an incredible amount of fumes is released. Zinc, with its lower melting point than other metals, quickly generates huge zinc fumes. We need to carefully extract and filter these fumes, otherwise our smelting facility will be filled with smoke. This is not only harmful to our employees but also to the residential area next to our factory. It means that we have to maintain air quality within the residential guidelines and work cleaner than what is customary in our industry."
Convenient vortex hood
Kiekens installed three Dustmasters DM10,000 for extraction. However, their filters are not resistant to very high temperatures. Therefore, Kiekens developed and installed a so-called vortex hood above the meltingprocess. This hood not only extracts hot smoke gases with dust but also draws in a certain amount of air from the surroundings. Thanks to the vortexprinciple, there is sufficient mixing of both airflows to evenly reduce the high temperature and ensure adequate extraction. The construction around the hood is also custom-made. During the melting process and maintenance work, the furnace needs to be easily accessible. Therefore, the hood was placed on rails so that it can be slid aside when the operator needs access.
Shaped by our unique approach
.webp)
Optimizing, expanding, and moving forward
Nevertheless, in 2021, the smelting facility discovered a capacity shortage. After adjusting the melting process and adding other additives for better results, the smoke generation significantly increased, pushing the existing extraction system to its limits. Therefore, alongside the existing Dustmasters, an additional Dustmaster DM10,000 was installed. The additional Dustmaster was connected to the vortex hood through a change overvalve, allowing for a total extraction capacity of 18,500 m³/h above the meltingprocess.
Reliable and low life cycle costs
Bob believes it was logical to build upon the existing extraction system: "Dustmasters are very reliable, simple machines that do their job efficiently. The life cycle costs are also low because the filters have a long lifespan. To illustrate, since the start of our smelting lab in2012, I have only had to replace the filters once. That is remarkably low, andi t was also done quickly. It was resolved within a day. With other systems, your production can be stalled for a week, making it a very expensive operation. n short, Dustmasters give me a worry-free existence, just like Kiekens. My account manager there has always taken care of me. So, in addition to the four Dustmasters here in Raamsdonkveer, we will soon have one in Oss and one in Krefeld. I think that says enough about how satisfied I am with this company and their extraction solutions."
Tailor-made solutions
We are true specialists. No work environment is the same, which is why we provide custom solutions. From filtration and ventilation to high-precision dust extraction that removes even the finest particles down to the last micrometer.
We also handle the installation of the piping system and all connections and provide ongoing service and maintenance. Kiekens is your one-stop shop and long-term partner for clean air, now and in the future.