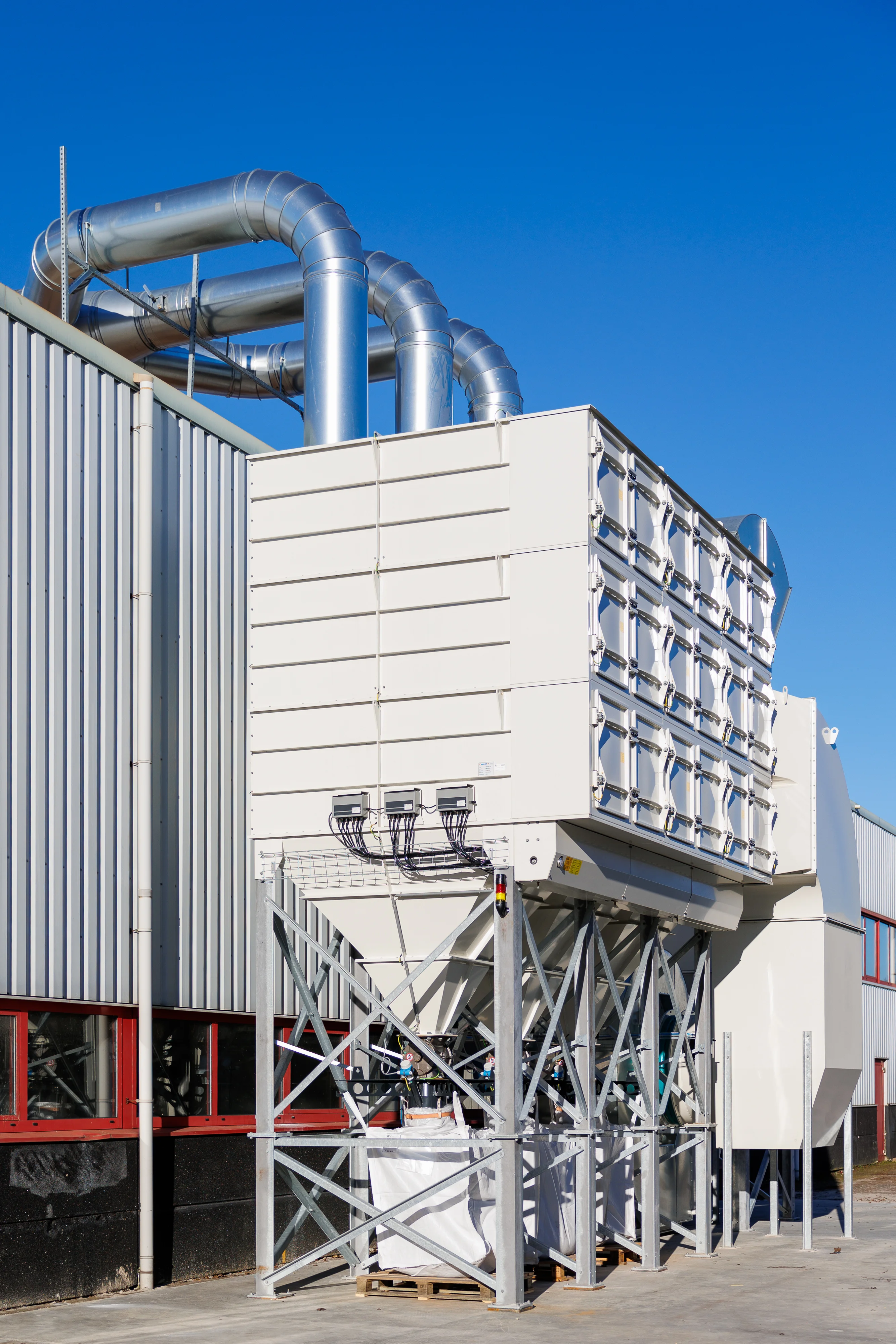
NNDI: "Dust Extraction is about taking care of your personnel"
The Noord Nederlandse Draadindustrie (NNDI) supplies high-quality wire steel in the form of steel wire, reinforcement steel, and wire nails from Dokkum. The construction and manufacturing industries use these semi-finished products in cars, various utensils, and for reinforcing concrete, among other applications. NNDI has a second branch in Beveren (Belgium) and a subsidiary in Uden where they produce galvanized steel.
The production of steel wire is a dusty job. When unrolling and feeding wire steel, the mill scale often breaks, releasing metal oxides as dust into the air. Although there was a dust extraction system in the production hall in Dokkum, it had become worn out and had not kept pace witht he growth of NNDI. So shortly after Ernst Dijkstra joined as the director, optimizing the dust extraction became a priority.
Being a good employer
Ernst explains, "Our employees were standing in a dusty working environment for eight hours a day. That's not healthy. Behind every production worker, there is a family, friends, and relatives. That comes with responsibilities, and that's what dust extraction is about, in my opinion. Our production area doesn't have to be a clean room, but from the perspective of safety and health, we needed to minimize the amount of dust in the air as quickly as possible."
Decisiveness, high level of expertise, and reassuring guarantees
"Through a mutual connection, our need for a new dustextraction solution reached Jeroen Roeleven, director of Kiekens, and he texted me just a minute later. I appreciated that decisiveness, but the matter was not settled yet. We also knew another supplier who could provide exactly what we needed. So why did we choose Kiekens? There were several reasons. Firstly, Kiekens' technical team came well-prepared. They were knowledgeable about what we do, brought materials to clarify certain aspects, and showed references of projects similar to ours. Furthermore, they deviated from the solution we had in mind. 'I hear what you're saying, but that won't work here,' explained one of the technical experts. It was clear that he had expertise in the field. The third reason for choosing Kiekens concerned the filters, our biggest concern. Filter elements wear out, and ideally, they should be replaced as late as possible. Albert Dorenbos, our account manager at Kiekens, guaranteed that the filters would last at least 5 years in our system, which operates 24/7. That was a reassuring promise and gave us the final push to go with Kiekens."
Shaped by our unique approach
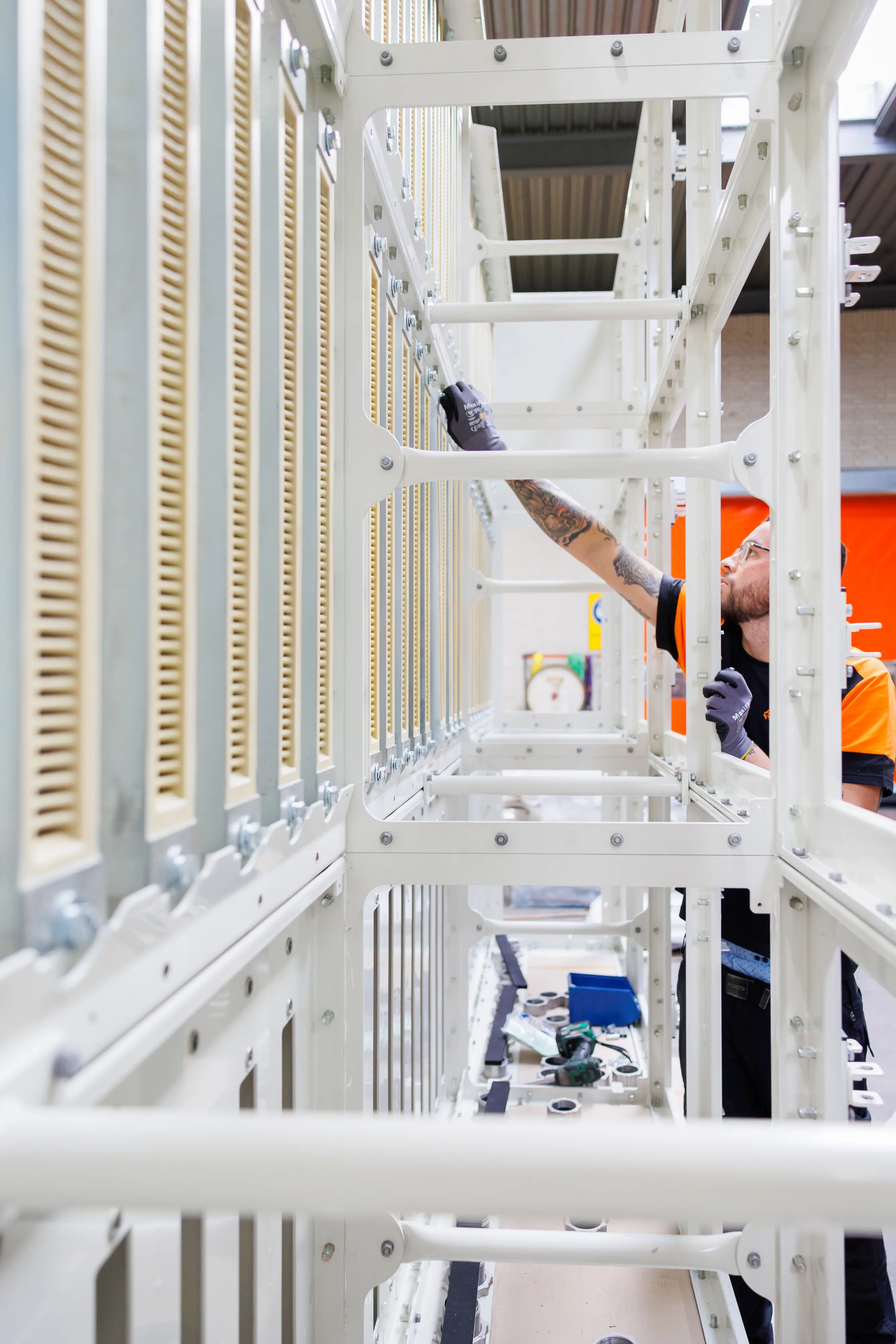
Customization with the Dustmaster DM20.000
"Albert advised us to go with the Dustmaster DM20.000. It is built in a modular way, providing a lot of flexibility. So we decided to place the Dustmaster outside. Albert and Eppie Weidenaar, manager of technology and innovation, then determined the pipeline route with the lowest possible resistance. The Dustmaster was given an extraction capacity of 50,000 m3/h. That is more than the 47,000 m3/h required by our 14 production machines, but it means we are prepared for the future in case additional extraction points are needed. Finally, our Dustmaster was equipped with high-efficiency filterelements with very low residual emissions. The dust extraction is now fully operational and meets our satisfaction. Since the Dustmaster is located outside, it was painted to match the color of the building. This led us to also consider potential noise disturbances: the extraction now operates at a frequency of 39 Hz. Air measurements conducted by Kiekens demonstrate that with an ample duct velocity above 20 m/sec, the released dust is adequately extracted. The extracted dust is neatly collected under the installation using three sluices and three big bags."
That's when I knew: it's in good hands
"In retrospect, I can say that Kiekens did a great job. But actually, I knew much earlier that we had made the right choice with them. In the initial phase, Kiekens provided clear answers to every question along with supporting visuals and graphs. And they kept their promises. Thatr esonates well with us Frisians. For example, there was a short delivery time, and it was achieved without great pressure or panic. Now that the Dustmaster is operational, we are extremely satisfied. The factory is pleasantly quiet, and employees say they come home cleaner nowadays. I also notice it myself when I walk through the production area: the air is much clearer; nothing is swirling around anymore. The Dustmaster has ensured a healthy and safe working environment - now and in the future - and I am very pleased with that."
Kiekens | Dustmaster DM 20.000 3/3 | Transport
Tailor-made solutions
We are true specialists. No work environment is the same, which is why we provide custom solutions. From filtration and ventilation to high-precision dust extraction that removes even the finest particles down to the last micrometer.
We also handle the installation of the piping system and all connections and provide ongoing service and maintenance. Kiekens is your one-stop shop and long-term partner for clean air, now and in the future.